
The degree to which the value stream is only processing products and services for which there is a customer demand, rather than creating something and hoping someone wants it. The degree to which there is smooth uninterrupted flow of activities that add value to the customer, rather than waste and inefficiency that impedes the flow through the value stream. The set of business activities and steps involved in creating and delivering products and services to the customer it is the connection of the steps together rather than considering each step in isolation. Value is determined by what the customer considers to be important within a product or service, rather than what the individuals developing or delivering the product or service consider important. Let’s take a look at the history of Lean Six Sigma, and how the different parts of this methodology were formed to become the process improvement approach we know today. Fortunately, the Lean Six Sigma approach to business improvement includes all three layers. An improvement process does not produce the desired results unless it includes the tools and techniques that define the activity of the process steps and there is a culture that insists on systemic data-based approach to solving problems.įinally, a culture that seeks to continuously improve will be frustrated if there are no tools and techniques for analysis and no process or methodology that can be applied to organize and focus the improvement efforts. Analytical techniques are not used effectively unless there is a process for applying them and a mindset of continuous improvement creating the need for them. These three elements reinforce each other. Mindset and culture: A way of thinking that relies on data and processes to achieve operational performance goals and continuously improve.
#Six sigma success story series#
Process and methodology: A series of phases that organize the use of the problem-solving tools to ensure that the true root causes are found and that a solution is fully implemented. Tools and techniques: A comprehensive set of tools and analytical techniques that are used to identify and solve problems. It is great to have TMAC as an organizational resource for DPS’ RCI transformation.There are three key elements to Lean Six Sigma. It empowers our people to make informed decisions when tackling change. “Our Lean Six Sigma based Rapid Continuous Improvement program is more than just a way to cut costs. Nosco is a firm believer in the MEP/TMAC program and their level of expertise.” “Lean Enterprise deployment and Six Sigma training have given our people a voice and they’ve practiced using that voice for the betterment of the business. – Rodney Schonefeld, National Operations Manager
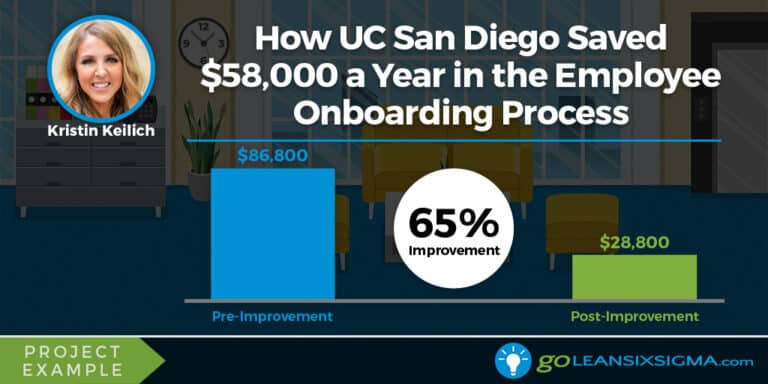
“The LSS training that we received from TMAC and the deployment of this program throughout our organization is resulting in a cultural change leading to continuous improvement activities netting bottom line results through improved quality, process efficiencies and customer service.” The new facility allows us to grow, and helps us to grow… Without TMAC’s assistance we would have laid the facility out wrong in a number of areas.” “It’s about bringing Fortune 500 companies in here who want to do business with us. – Joel McKnight, Assistant Parks and Recreation Director “Over the first 12 months of these improvements being in place results only varied 7% month-to-month…”
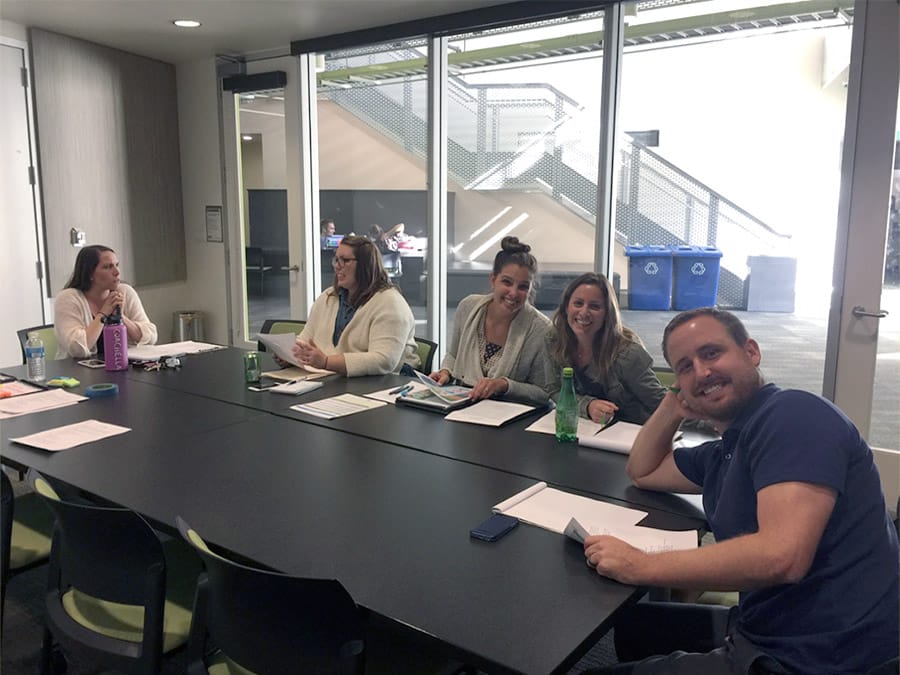
– Richard Bristol, Deputy Director Project #3: Irrigation Repairs “Lean Six Sigma training received from TMAC has been instrumental in helping the City of El Paso achieve unprecedented service improvements and cost savings in many of its departments…” – Mary Gamez, Green Belt Team Member Project #2: Asphalt Repairs
#Six sigma success story how to#
You have no idea how great it is to be involved in working through the process and helping make the changes instead just being told how to change things.” “I just want to say thank you for giving me the opportunity to be a part of the Lean Six Sigma improvement team. I measure the true success of the project by the positive comments that we hear from customers and staff.”Ĭity of El Paso: Project #1: Parks and Recreation “The LEAN Forward Project was the best thing that we could have done.
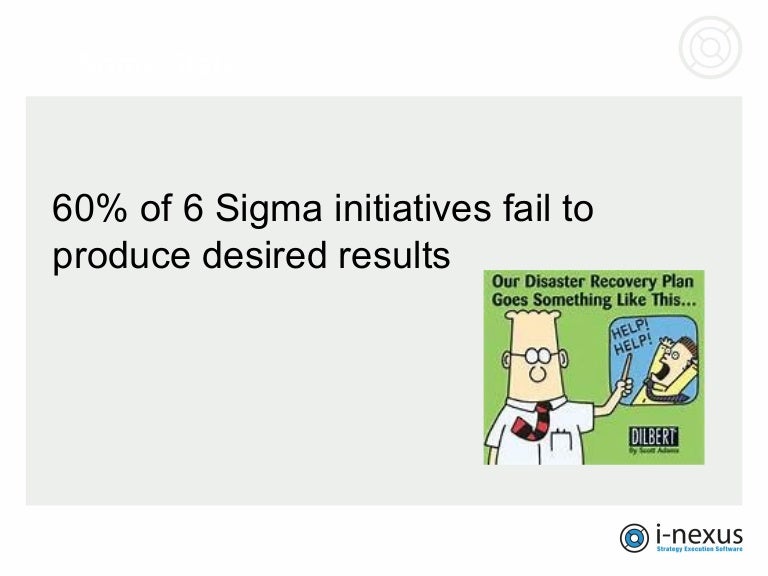
“Working with TMAC to integrate the LSS methodology throughout our company has had an incredible impact on our organization. TMAC has been integral in the training and development of our Black Belts and Master Black Belts, and continues to be a valued contributor on our journey of continuous improvement.” TMAC helped point them out and then worked with us to eliminate them. It was a little embarrassing to see all of the wasteful practices that crept into our production line over the years. “TMAC was key to helping InterConnect Wiring vastly improve our kit manufacturing line. We’ve served customers all across the US.
